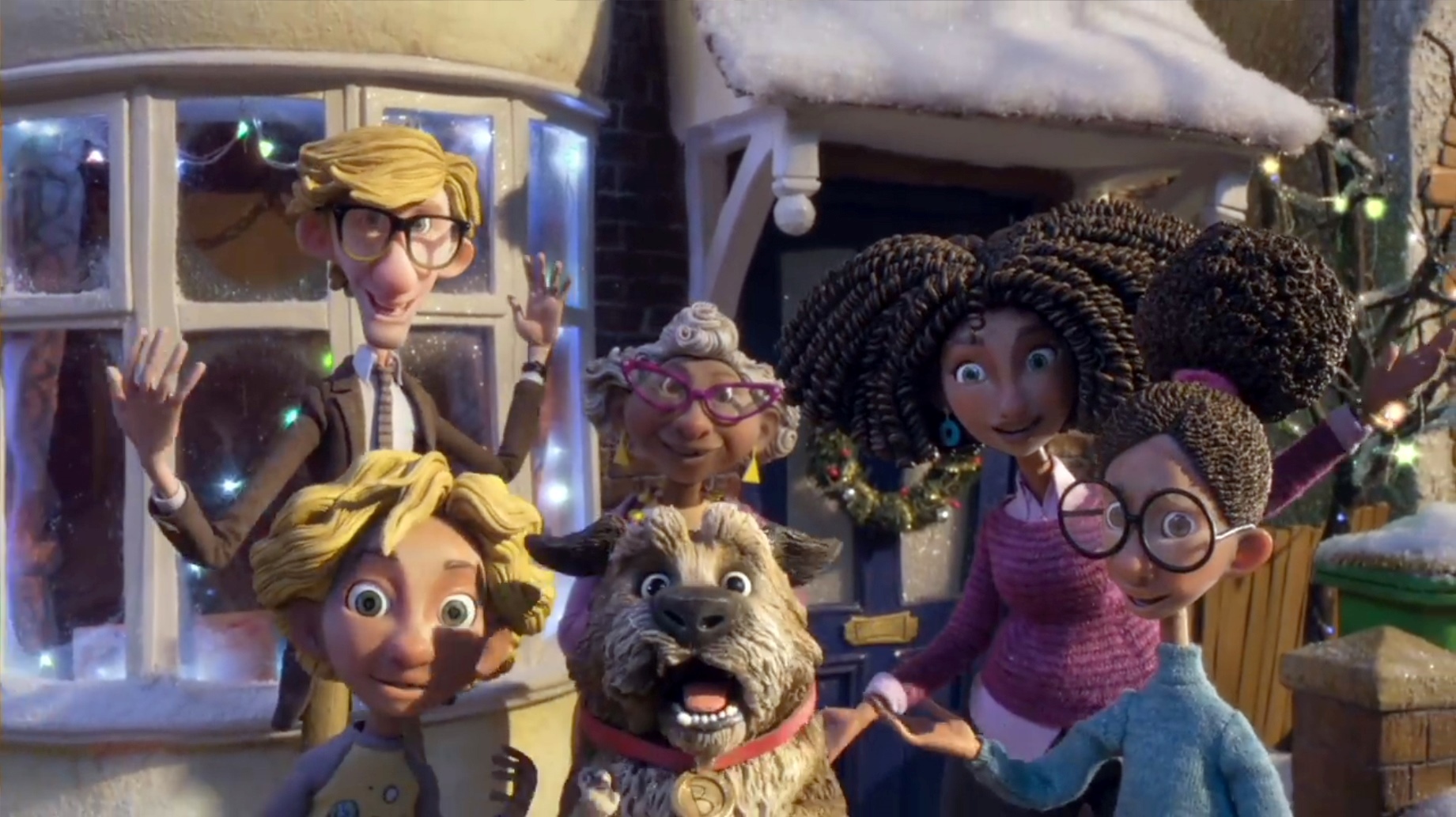
The Greatest Gift
As the first snow falls, we find our hero Dave caught up in the Christmas whirlwind – all he wants to do is to get home to spend time with his family, but all sorts of Christmas duties and calamities are getting in his way. That is until he sees a gingerbread man on his daughter’s bedside table that they’ve made to look like him. That gives him a genius brainwave…
Watch the advert here!